In the age of Industry 4.0, operational efficiency is no longer a competitive edge—it’s a baseline expectation. Manufacturers and facility managers are under increasing pressure to maximize uptime, reduce maintenance costs, and optimize equipment performance. Enter wireless sensors–a transformative technology that’s rewriting the rules of industrial machinery maintenance.
The High Cost of Downtime
Unscheduled downtime in industrial settings can cost companies thousands—or even millions—of dollars per hour, depending on the scale of operations. Beyond the direct financial impact, downtime also strains human resources, disrupts production schedules, and damages customer trust. Traditional maintenance models—such as reactive and scheduled maintenance—often fail to catch problems early enough or result in unnecessary downtime due to over-servicing.
The Wireless Sensor Revolution
Wireless sensors provide a smarter, more efficient alternative. By continuously monitoring key parameters like vibration, temperature, electrical current, and air quality, these sensors deliver real-time insights that empower predictive and preventive maintenance strategies.
Key Advantages:
- Non-Invasive Installation: Wireless sensors are easy to install without the need for complex wiring, minimizing disruption during deployment.
- Scalable Monitoring: Facilities can scale sensor networks across multiple machines and locations without significant infrastructure changes.
- 24/7 Real-Time Data: Continuous monitoring allows maintenance teams to detect and address anomalies before they become failures.
- Remote Access: Cloud-based platforms enable technicians and managers to monitor machinery health from anywhere, boosting responsiveness and decision-making speed.
Predictive Maintenance in Action
Let’s consider a manufacturing plant using wireless vibration sensors on its CNC machines. Normally, identifying spindle bearing wear would rely on scheduled manual inspections. But with sensors in place, vibration anomalies are automatically detected and flagged when they deviate from baseline norms. Maintenance teams can then intervene precisely when needed, preventing costly breakdowns and extending machine life.
Another example involves wireless temperature and current sensors monitoring motors and compressors in an HVAC system. Any rise in temperature or drop in efficiency is instantly recorded and alerts are generated, enabling timely maintenance that prevents system failure.
Data-Driven Insights for Long-Term Gains
Wireless sensors don’t just prevent downtime—they also help organizations optimize their long-term maintenance strategies. By analyzing historical sensor data, facilities can identify recurring issues, adjust maintenance schedules, and even influence equipment procurement decisions. This transition to a data-driven maintenance culture fosters continual improvement and cost savings.
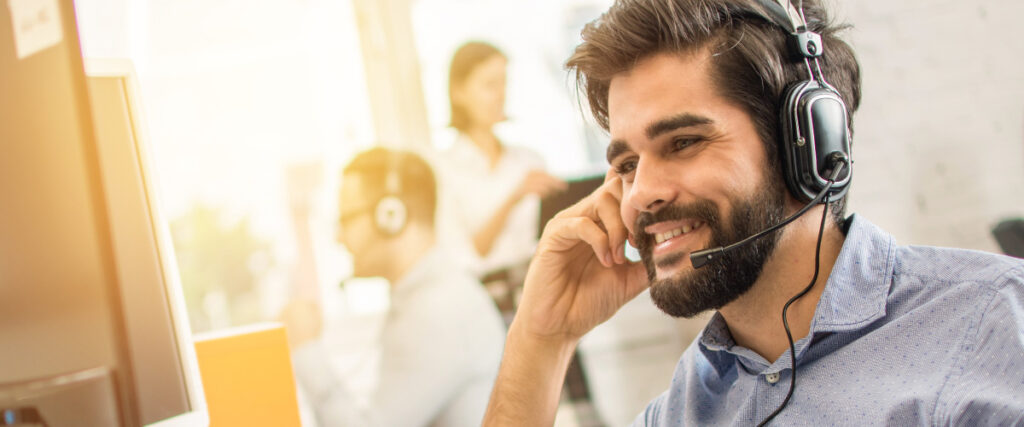
Talk with a Specialist
If you think it can’t be monitored, contact us, we might surprise you.
Why Swift Sensors?
At Swift Sensors, we specialize in delivering cutting-edge wireless sensor solutions tailored for industrial applications. Our sensors cover a wide range of needs, including:
- Vibration sensors for predictive maintenance of rotating equipment.
- Temperature and humidity sensors for environmental control.
- Current and voltage sensors for electrical monitoring.
- Water leak and door open/close sensors for infrastructure safety.
All data is securely transmitted to a cloud dashboard, where customizable alerts, analytics, and reporting tools provide actionable insights at your fingertips.
The Future is Proactive
Industrial facilities no longer need to choose between uptime and affordable maintenance. Wireless sensors for industrial manufacturing make it possible to be proactive instead of reactive, ensuring machines run longer, maintenance is smarter, and operations are leaner. For organizations aiming to stay competitive in an increasingly connected world, embracing this technology isn’t just an option—it’s a necessity.
Stay in the Know with Swift Sensors
Sign up for the Swift Sensors newsletter to stay ahead in sensor technology. Get exclusive updates on industry trends, product releases, and special promotions. Elevate your knowledge and be part of our tech community. Signup now!